Präzision macht blau
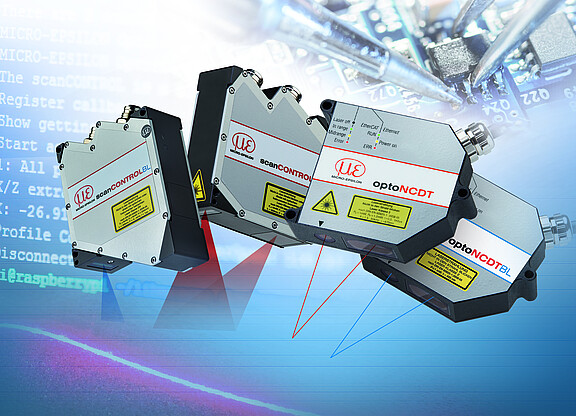
Optische Messverfahren spielen eine entscheidende Rolle bei der zunehmenden Automatisierung von Fertigungs- und Prüfprozessen. Mit modernsten Verfahren der Laser-Triangulation werden Verfahrwege, Maschinenpositionen und produzierte Bauteile vermessen und deren Messpunkte schnell, hochpräzise und sicher aufgenommen. Abhängig von den erforderlichen Eigenschaften der jeweiligen Anwendung arbeiten diese Sensoren mit rotem oder blauem Laser.
Mit dem Triangulationsprinzip werden Abstände gegen ein breites Spektrum von Materialoberflächen gemessen. Dabei kommen verschiedene Messverfahren zum Einsatz: Die Messung von Weg, Abstand und Position per Laserpunkt-Triangulation und die Profil- und Spaltmessung per Laserlinien-Triangulation. Die Sensoren können mittlerweile mit roter oder blauer Laserlinie ausgestattet werden. Jeder der beiden Lasertypen hat seine ganz eigenen Vorteile und auch Grenzen.
Der rote Laser ist seit den 90er Jahren eine bewährte Technologie in der Messtechnik, die für viele Anwendungen in unterschiedlichsten Branchen schnelle und hochgenaue Ergebnisse liefert. Micro-Epsilon entwickelte die Technologie des roten Lasers weiter und präsentierte vor einigen Jahren eine Weltneuheit: die Blue-Laser-Technologie, die zunächst in Laser-Punkt-Sensoren zum Einsatz kam. Die Blue-Laser-Technologie kommt in der Regel dann zum Einsatz, wenn der rote Laser seine Grenzen erreicht. Das blaue Licht dringt im Gegensatz zum roten nicht in das Messobjekt ein und bildet einen scharfen Punkt bzw. eine scharfe Linie ab. So können vor allem organische oder semitransparente Objekte zuverlässig vermessen werden. Insbesondere bei glühenden Objekten hat der blaue Laser Vorteile. Er bietet einen maximalen spektralen Abstand zum Infrarotlicht und zeigt sich daher unempfindlich bei roter Strahlung, wie sie beispielsweise bei glühenden Metallen auftritt. Sensoren mit rotem Laser liefern bei rot glühenden Metallen fehlerhafte Signale, da der hohe Anteil der infraroten Strahlung das Sensorelement beeinflusst.
Die Lasersensoren mit rotem Laserlicht sind dagegen auch mit höheren Laserklassen verfügbar und liefern eine höhere Lichtintensität als das blaue Laserlicht. Rot ist damit vor allem bei dunklen Oberflächen besser geeignet. Besonders deutlich wird dies bei frisch extrudiertem, schwarzem Reifengummi, der viel Licht absorbiert. Das blaue Laserlicht wird von der schwarzen Oberfläche „verschluckt“, während das rote Laserlicht ausreichend reflektiert. Bei glänzenden Metallen und rauen Oberflächen sind mit dem roten Laser mehr Informationen zur Bildung eines Mittelwerts abrufbar, während das blaue Licht bei glatten Oberflächen genauere Ergebnisse zulässt.
Im Allgemeinen ist für jeden Anwendungsfall zu prüfen, welches Laserlicht für die vorgegebene Messaufgabe idealer geeignet ist und in Folge präzisere Ergebnisse liefert. Abhängig vom Messobjekt dringt bei herkömmlichen roten Lasern das Licht in das Messobjekt ein. Je nachdem, aus welchem Material das Messobjekt besteht, tritt dieser Effekt weniger stark oder verstärkt auf. Das ist gerade bei organischen Messobjekten der Fall, bei denen das rote Laserlicht aufgrund der Wellenlänge deutlich in die Oberfläche des Messobjekts eindringt und dort gestreut wird. Dadurch wird an der Oberfläche kein scharfer Laserpunkt oder eine scharfe Laserlinie abgebildet, was die Ermittlung des Abstandes erschwert. Das blau-violette Laserlicht dringt durch seine kürzere Wellenlänge im Vergleich zum roten Laser kaum in das Messobjekt ein. Der blaue Laser sorgt damit für stabile und präzise Ergebnisse auf Messobjekten, bei denen der rote Laser an seine Grenzen stößt.